At a glance
- Despite mining’s environmental impact, it remains a key future industry because minerals are vital to infrastructure and development.
- The Paris Agreement goal of net zero emissions by 2050 emphasises the importance of mining over the next few decades.
- Mining robots, automation and small nuclear reactors may be the way of the future, along with cleaner, more transparent and responsible mining practices.
Walk onto a mine site a decade or two from now and you’ll likely see far fewer people, says Professor Nigel Cook, director of South Australia’s Premier’s Research and Infrastructure Fund.
In fact, you might not see a mine at all, at least not as we know it. Instead, the mine could be non-invasive, using innovative bio-leaching processes that mean the ore doesn’t have to come out of the ground in the traditional way.
“There will be mining robots, more electrification and computers will be running things,” says Cook, who is also a professor in the School of Civil, Environmental and Mining Engineering at the University of Adelaide.
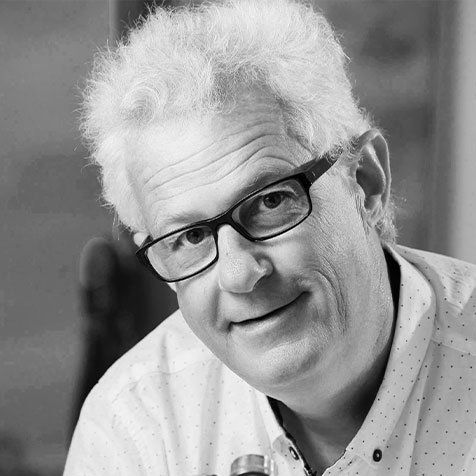
“Many of the electric lines of machinery will be supplied by renewables. Some mines might be powered by small, nuclear power reactors as a stopgap on the way to a full renewable future.”
Brett Triffett, transformation technologist at OZ Minerals, says the disruptive change in the energy, transport and mining sectors will only accelerate as we work towards decarbonisation and a sustainable supply of raw materials.
“What was driving innovation in the past is different to what is driving innovation today and into the future,” Triffett says.
“OZ Minerals produces copper, which is needed in electric vehicles and infrastructure, as well as in household appliances like fridges.
As demand for copper grows, we are also seeing a push for these metals to be mined transparently and responsibly.”
Companies such as Apple, Tesla and Mercedes are making public their efforts to improve the responsibility and traceability of source feed materials, Triffett says.
“In 2019, the London Metal Exchange [LME] released its responsible sourcing requirement to ensure the metals traded on the LME are responsibly produced,” he says.
However, when it comes to the radical change on mine sites described by Cook, much of it can only happen once we educate an entirely new generation of mining professionals. They will have to embark on setting up a new, sustainable mine from scratch, he says.
“We’ve got a lot of work to do in selling these ideas to the general public and to the government,” he says. “Mining is environmentally bad, on that we all agree. But mining has to be part of the solution.”
Indeed, the paradox of sustainability is that mining is likely the single most important factor of the zero-emissions solution.
The copper conundrum
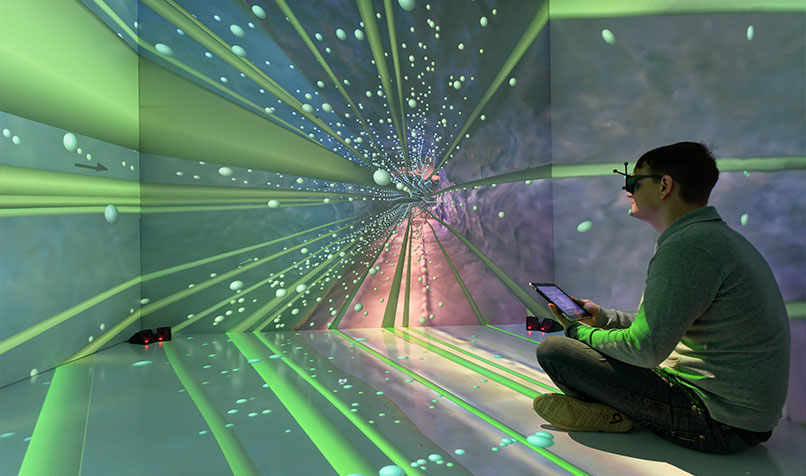
The Paris Agreement goal of net zero emissions by 2050 means mining will be more important than ever over the next few decades.
“We all want to move away from a fossil fuel based system,” says Professor Michael Goodsite, director of the Institute for Sustainability, Energy and Resources at the University of Adelaide.
“We’re going from a society powered by liquids that come from underground to a society that’s powered through metals and other materials that also come from underground.”
Goodsite says an average-sized, land-based, energy-producing windmill uses about eight tonnes of copper in its construction. An average wind farm has about 100 of these windmills. To replace the energy from one standard, coal-fired power plant, about 17 wind farms are required.
To produce the eight tonnes of copper for just one windmill, about 110 tonnes of ore must be mined, and that’s not even taking into consideration all the other metals required to build a windmill.
“So one wind park requires a very large amount of copper leading to a large mine or mines,” Goodsite says. “Solar cells need metals, too. Batteries need metals. Even hydrogen production can require certain types of metals.
"The International Energy Agency has done a study of what it will take to meet the net zero commitments by 2050. Putting the amount that they need into perspective, the amount of copper needed means we must mine more copper in the next 28 years than we have mined in the history of humankind. That’s a lot of copper, especially given there are no known efficient substitutes for all of the uses of copper.”
Can we achieve green mining?

Given the current context, an increasingly strong theme in mining is to find lower footprint solutions, Triffett says.
“For many years now, ore grades have been falling across the industry,” he says. “If we do nothing and stick with traditional methods of mining and processing, we’re just going to create larger volumes of waste and be reliant on increasing amounts of energy.
“As we look at designing modern mines, we’re going to need to get creative to find new solutions.”
Triffett is part of the Think and Act Differently (TAD) team at OZ Minerals, tasked with exploring opportunities that global challenges will create for the company, its clients and its stakeholders.
“For the TAD team, this includes learning from other industries and people who may not normally be in our ecosystem,” he says.
Last year, TAD launched the Ingenious Extraction Crowd Challenge, with innovators completing their experiments this year. Its aim is to test ideas that might disrupt traditional extraction processes and move towards lower-impact onsite metals production.
“We invited innovators to propose novel leaching processes that could demonstrate material changes in key economic drivers such as energy usage, while maintaining metal recovery rates equivalent to the incumbent systems,” he says.
"If we do nothing and stick with traditional methods of mining and processing, we are just going to create larger volumes of waste and be reliant on increasing amounts of energy. As we look at designing modern mines, we're going to need to get creative to find new solutions."
Amazingly, 260 participants from 40 countries took part in the challenge. The TAD team selected seven teams as finalists, each proposing new and innovative extraction systems. Various experiments have now been funded to validate the performance of these processes.
It is good news that such innovative programs are happening now. In the past, however, organisations in the mining space have been accused of being slow to change; and they have been, Cook says.
Cook acknowledges that in some cases change has been slow, but he argues that this is understandable. After all, a very large capital investment goes into exploration, mine development, mining operations and the transport and processing of ore.
Also, mining is such a broad and complex sector that it is difficult for an expert in one area to comprehend what is going on in others.
“Very few people in mining have a full perspective over the whole mining value chain,” Cook says. “They don’t necessarily have the economic viewpoint. Geologists don’t understand processing, processors don’t understand geology, etc.”
However, according to Cook, environmental, social and governance issues are paramount in the industry right now. The process of applying for a mining licence can take one to two decades, so optimisation of all parts of mining processes is essential.
Goodsite agrees, saying the Holy Grail of mining is the reduction of energy and water usage.
“Most copper mines are only mining the top 5 per cent or 10 per cent of the copper that they have in the reserves, because the rest is too deep or too complex to get to,” Goodsite says.
“To resolve that, miners generally have to add more energy and water, and the processing of these ores to get the metals requires a lot more energy.”
Indonesia is looking into using nuclear power for the energy-intensive processing phase, he says. Iceland uses geothermal power.
“Australia could have some variable renewable energy to generate an energy vector, like hydrogen, then use hydrogen for processing,” Goodsite says. “In my opinion, hydrogen has to be a part of the solution. And luckily, in Australia we do hydrogen very well.”
CPA Australia resource
What is bio-leaching?
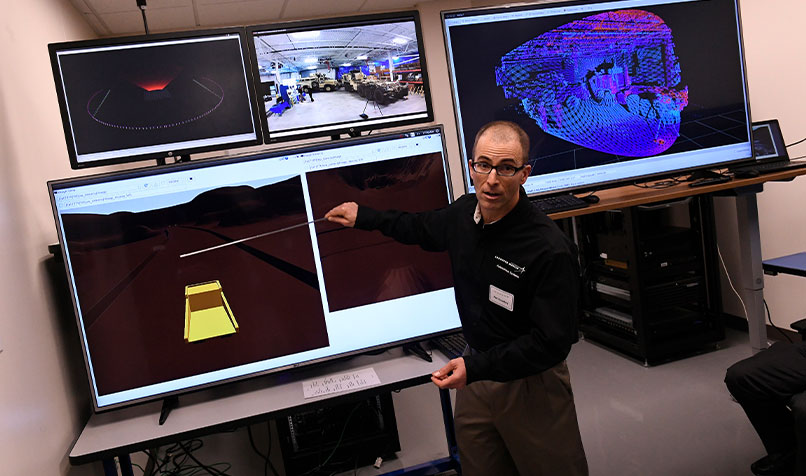
One of the potential future solutions to make mining more environmentally friendly is to copy what nature does, but find ways to speed up the process. This reduces the amount of physical energy required and instead uses biological energy.
“The process called leaching uses bacteria that generate acids, and the acids leak through whatever you mined and the copper, for example, is dissolved,” Goodsite says. “Then, at the bottom, you suck up the copper. You haven’t had to spend energy crushing ore.”
"Australia could have some variable renewable energy to generate an energy vector, like hydrogen, then use hydrogen for processing. In my opinion, hydrogen has got to be a part of the solution. And luckily, in Australia we do hydrogen very well."
Researchers know about this process now. The problem is that it takes nature 15 to 20 years to leach materials.
“The question is whether there’s a way to catalyse that,” Goodsite says. “Can we make nature work even better? Because if we’re doing that, we’re using nature’s own energy instead of something we have to produce.”
Where does technology fit in?
Professor Nigel Cook sits on the governing board of the integrated mining consortium, a research body that applies data analytics, machine learning, industrial internet of things and advanced sensing to improve mining operations and mineral processing.
“In general, we’re trying to make the whole operation a lot more efficient,” says Professor Nigel Cook from the University of Adelaide.
“Machine learning with artificial intelligence can make dramatic cost savings if they’re implemented by end users.
“It can be as simple as clever software that helps with stockpiling ore and enables better blending, so you can better protect the characteristics of the ore that is sent to the plant. It means higher recoveries using less energy and less water.”
None of this change is easy, but experts agree it is essential.
“It is not a simple matter of bolting on a solar plant to existing equipment,” Triffett says.
“Rather, there are opportunities to redesign the whole mining value chain, from exploration to extraction to processing, so we can leverage new types of energy and the opportunities and challenges this will bring. Modern mines will look different from how they look today.”