At a glance
For decades, Japan has topped the Atlas of Economic Complexity, a Harvard Growth Lab measure of the complexity of products manufactured in and exported by 133 countries.
In making cars, photographic equipment, electronics, computers, robots and more, Japan has a diverse mix of technological know-how and real manufacturing capability.
Australia, on the other hand, has dropped in the list from 55 in 1995 to 91 in 2020. With low-complexity export categories, such as minerals and agriculture, Australian manufacturing capability pales in comparison to most other countries.
Paul Cooper FCPA, chair of the Advanced Manufacturing Growth Centre and owner and executive chair of industrial electronics manufacturer Rinstrum, says that products exported by Japan have a high degree of complexity.
“The US and Korea are up there near the top of the table,” Cooper says. “Germany is up there, too. Then you get to Australia, and the first item listed that has a large amount of manufacturing input is wine.
"I know Germany is nestled in Europe, and there are about half a billion people around them, but we should be able to do it, too. We have proven we could, in the past.”
The Advanced Manufacturing Growth Centre, established in 2015, aims to transform Australian manufacturing, to make it globally competitive and innovative. A booming manufacturing sector can create jobs, while the economy would become healthier and more resilient.
“Australian manufacturers need to be using data analytics to understand what the market and the production processes are telling them,” Cooper says.
“How do we tweak what we do to become globally competitive? What data can we use, from the factory floor to where the product is being used, to influence the production process?
"How do we boost efficiency, speed, performance and quality? It is all about smart manufacturing. Being an advanced manufacturer is not what you make, but how you make it.”
Define "smart"
Jannat Maqbool CPA, APAC principal adviser at Ecosystm, innovation partner at Aurecon and member of CPA Australia’s Digital Transformation Centre of Excellence, says that the use of the term “smart” in “smart cities” signals the leveraging of data and technology for “whatever you want the city to do for its inhabitants”.
“Manufacturing is the same thing,” Maqbool adds. “It is known as ‘Industry 4.0’. It is about the level of maturity of an organisation’s technology, including the use of AI, the Internet of Things, big data, etc. It is about efficiency, cost reduction, innovation and having less of a footprint in terms of the environment.”
Monash University engineering lecturer Dr Yunlong Tang says that smart manufacturing is also about making the end product smarter.
“It means we do not just manufacture the hardware,” says Tang. “We also develop and sell a smart service based on the product we manufacture.”
Well-executed smart manufacturing can help a manufacturer to compete and be profitable even in territories with high labour costs, such as Germany and the US, Tang says.
Keep it simple
Professor Adrian Neild, deputy dean of strategic initiatives in the Faculty of Engineering at Monash University, says that digitising manufacturing processes can give a business an immediate overview of how each of its machines is operating.
This may help a business to identify if urgent maintenance is required before faulty products slow down or stop the production process.
“You can integrate quality control steps within that process, have much faster feedback to make alterations, and waste less materials and time,” Neild says.
“There are also industries in which provenance is important. Smart manufacturing can produce digital evidence as quality assurance for those products. Biomedical and pharmaceutical products are obvious examples.”
Does this involve replacing all the current machinery with shiny, new digital versions? No, says Cooper.
For instance, Australian business called MOVUS has developed a smart monitor that clips onto the side of existing machinery and constantly monitors vibrations, noise, temperature and more.
“This device has a whole lot of smarts in it,” Cooper says. “It reports back to a central control room that is monitoring thousands of machines around Australia. It uses conditionbased, predictive monitoring to predict failures.
“It will tell the owner when parts start to overheat, are becoming noisy or vibrating out of range, and that they need to do some maintenance before it becomes a real problem. It saves companies hundreds of thousands of dollars.”
Avoid tech for tech's sake
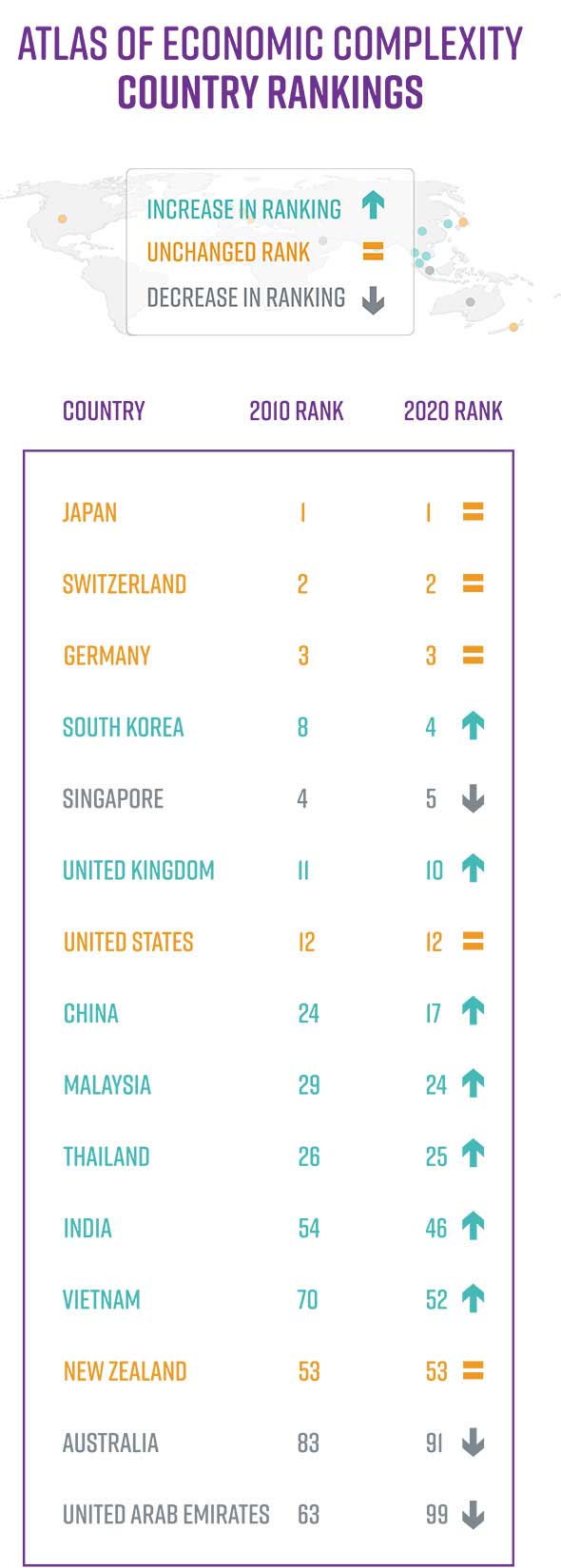
More than 860,000 people are currently employed in manufacturing in Australia by about 47,000 manufacturers. Almost 90 per cent of these businesses have fewer than 20 employees.
If even a small percentage of these manufacturers become more competitive and grow – exporting knowledge as well as products – there could be sizeable economic and employment benefits.
EDARC, another Australian manufacturer, has created about 35 new jobs by also employing robots and co-bots, Cooper says.
“Staff are not doing heavy lifting or mundane and easily repeatable tasks, so they have been able to boost their production and the company has grown,” he says.
Brisbane business UAP creates art projects for global clients. Some of those pieces are six storeys tall. In their workshops, they use augmented reality (AR) to bring their art to life and make essential design changes, all before they begin production of the real thing.
“They wear goggles as they stand on the massive factory floor with nothing in front of them, and they are pointing, touching and marking things virtually,” Cooper says.
“When you put the goggles on you see the massive artwork. In the virtual world, the artists have it lying down.
They’re walking alongside it, drawing on parts of it, marking connection points and circling problem areas. It is fascinating.”
Maqbool says that risk also comes with every major change. “There is a real danger in businesses not thinking deeply enough, just changing what they currently have so it is automated,” she says.
“But that just means they are replicating their current processes.
“It is not about saying, ‘Here’s a technology, I’m going to apply it’. It is about knowing what the business needs. What is the next stage it wants to reach in the short term, medium term and long term?
“If you want to amp up production but labour is difficult to find, how can we produce 100 widgets out of this machine each day instead of 50? If you want greater speed to market, where can most time be saved by utilising technology? If quality is a focus, how can the quality control process be improved?” says Maqbool.
Smart manufacturing should be about the business, its end goals and its market, rather than the technology itself, she says. It should also take stakeholders along on the journey, including accountants and technology partners who will “stick with you over the long run, developing a strategic technology and data roadmap aligned with business goals and supporting capability development, compliance and innovation”.
The global perspective

Smart manufacturing is used globally for any and every purpose.
Some organisations, Tang says, are building a digital twin of their current plant. BMW in Germany uses a digital twin to experiment with process, materials and other changes to ensure that when they make a change in the real world it is the best option.
Quality control is another use for smart manufacturing. One manufacturer, Tang says, was receiving complaints about defects in their final product. The company’s smart processes helped them to identify the problem as being in the transport of the goods and not in the manufacturing process.
"These technologies can be integrated with existing worker practices. This is not about replacing people. It is about securing the future for this type of activity within first-world economies."
Increasing numbers of factories are using fully autonomous, automated collaborative robots – or “co-bots” – that are designed for human–robot interaction. Co-bots can carry out repetitive, relatively low-value tasks, co-working with their human counterparts who have their time freed up to work on higher-value, more creative tasks.
“This reduces labour costs, improves product quality, creates a safer and more engaging working environment and makes manufacturing more sustainable,” Tang says.
“These technologies can be integrated with existing worker practices,” Neild says.
“This is not about replacing people. It is about securing the future for this type of activity within firstworld economies.”
From Smart Cities Initiative to Ecosystm, Jannat Maqbool CPA holds many roles
Scaling up
Skill set is the biggest challenge in the growth of smart manufacturing, Neild says, in terms of knowledge about what is achievable and the skills needed to implement those options.
The key skills are “predominantly engineering and IT-associated skills – in robotics, cyber security, AI, data handling, programming and data analysis”, says Neild.
The regulatory environment is also important, Tang says, particularly around data safety. “In manufacturing, we will need to protect IP and protect data.
“Another regulatory point is safety. In the past, we have put robots in a steel cage for safety reasons. Now, more autonomous robots will be working with humans. We will need to push forward on standards and regulation to support the safety of the working environment,” Tang says.
The need to better understand smart manufacturing technology and how it can interact with processes is crucial. Once there is a good understanding of what can be achieved with smart manufacturing, there will also be a greater appreciation of how such a short-term investment will bring long-term gain, Neild says.
“When a new technology comes along, you can approach it with fear that you will be left behind, or you can embrace it as an opportunity,” Neild says.
“In Australia, there is now good awareness that this is the way we have to go. There are numerous examples of companies that have done so. We are on the brink of something great.”